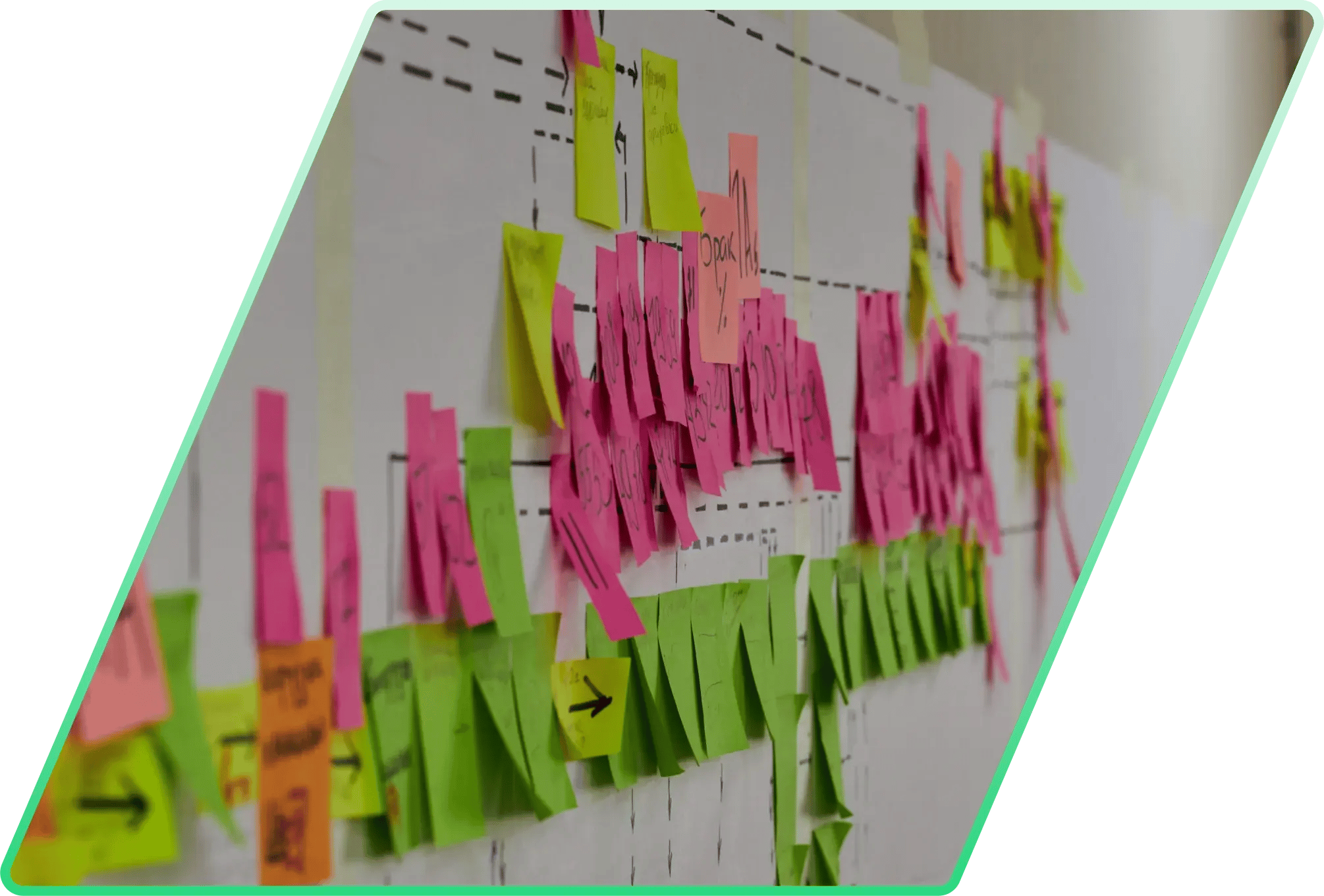
Operations Lean Tools
Transform Your Operations With Industry Leading Lean Tools
Our Operations Lean Tools empower your team to optimize every aspect of your production processes. From Value Stream Mapping to Visual Management, these tools are designed to streamline workflows, reduce waste, and drive exceptional productivity on the shop floor.
Solutions
Operations Lean Tools
- A3 Problem Solving
- Standard Work Training
- Learning to See
- Kanban Workshop
- Value Stream Map Training
- Quick Changeover Workshop
- Quality Stream Map Training
- Total Productive Maintenance — TPM
- Visual Management
Overview
A3 Problem Solving
Problem Solving by everyone in an organization is the core of any Lean Enterprise culture. Kaizen is the ability to understand the problem and apply problem-solving techniques in pursuit of perfection. This workshop features a “teach & do” format. Participants will receive training in how to drive to the ultimate root cause of problems rather than attaching short-term “band aid” action to the problem that wastes time and money.
Benefits
- Root Cause Identification: Develop the skills to identify and address the root causes of problems, rather than applying short-term fixes.
- Structured Problem-Solving Approach: Gain proficiency in using structured problem-solving techniques such as 5 Why Analysis, Fishbone Diagrams, and PDCA (Plan, Do, Check, Act).
- Improved Process Efficiency: Learn to standardize processes and implement robust countermeasures that prevent problems from recurring, leading to more efficient and reliable operations.
- Enhanced Decision-Making: Utilize A3 worksheets to document and analyze problems, improving decision-making and strategic planning within the organization.
- Cross-Functional Application: Apply problem-solving techniques across various departments, including the office, plant floor, and supply chain, fostering a culture of continuous improvement throughout the organization.
- Increased Employee Engagement: Empower frontline workers, administrators, and managers to actively participate in problem-solving, leading to greater ownership and accountability in the improvement process.
- Actionable Insights: Visualize existing problems and identify key areas for improvement, providing a clear path forward for implementing effective solutions.
Learning Objectives
- Master Root Cause Analysis Techniques: Learn to apply root cause analysis techniques, including 5 Why Analysis, Fishbone (Ishikawa) Diagrams, and 4M Analyses, to uncover the underlying causes of problems.
- Effectively Use A3 Problem-Solving Tools: Gain the ability to document, standardize, and archive problem-solving processes using A3 worksheets.
- Apply Poke Yoke (Error Proofing) Techniques: Understand and implement Poke Yoke techniques to prevent mistakes and ensure quality in processes.
- Standardize Processes Using PDCA: Learn to apply the PDCA (Plan, Do, Check, Act) cycle to standardize processes and ensure continuous improvement.
- Develop and Implement Countermeasures: Acquire the skills to develop robust countermeasures that eliminate recurring problems and enhance process reliability.
- Comprehend 5W1H Analysis: Understand and apply the 5W’s and 1H (Who, What, Where, When, Why, and How) method to thoroughly analyze problems and identify actionable solutions.
- Visualize and Plan for Improvement: Learn to visualize existing problems within processes, identify areas in need of improvement, and outline actionable plans for future enhancements.
Overview
Standard Work Training
The Standard Work Training is designed to equip participants with the essential knowledge and practical skills needed to create and implement Standard Work within their organization. This workshop follows a "teach & do" format, where participants will learn the three core elements of Standard Work: Takt Time, Work Sequence, and Standard Work in Process (SWIP). Through hands-on exercises and the development of Standard Work documents, attendees will gain the ability to streamline processes, reduce variability, and support continuous improvement efforts. This training is vital for any organization seeking to improve operational consistency, enhance safety and quality, and establish a foundation for ongoing process excellence.
Benefits
- Simplified Training of New Workers: Standard Work provides clear, documented procedures that make it easier and faster to onboard and train new employees, ensuring they quickly become productive members of the team.
- Reduced Process Variability: By standardizing work processes, this training helps to minimize variations, leading to more consistent quality and reliable outcomes across all operations.
- Enhanced Safety and Quality: Implementing Standard Work reduces the likelihood of errors and accidents, contributing to a safer workplace and higher quality products or services.
- Foundation for Continuous Improvement: Standard Work serves as a baseline for identifying inefficiencies and opportunities for kaizen (continuous improvement), enabling ongoing enhancements to processes.
- Improved Visual Management: Participants will learn how to use visual management techniques to monitor and sustain Standard Work, making it easier to identify deviations and maintain process discipline.
Learning Objectives
- Understand the Core Concepts of Standard Work: Participants will learn the key elements of Standard Work, including Takt Time, Work Sequence, and Standard Work in Process (SWIP).
- Differentiate Between Standard Work and Work Standards: Gain the ability to distinguish between Standard Work, standardization, and work standards, and understand their unique roles in process improvement.
- Perform Direct Process Observations: Learn how to conduct direct process observations to measure cycle times accurately and identify opportunities for improvement.
- Create Standard Work Combination Sheets: Develop the skills to create Standard Work Combination Sheets (SWCS) that document the sequence of operations, balancing work to takt time.
- Develop Standard Work Sheets: Understand how to create and utilize Standard Work Sheets (SWS) to document procedures and ensure consistency across operations.
- Implement and Audit Standard Work: Learn to use Standard Work documents for training, process improvement (kaizen), and visual management, ensuring continuous adherence and improvement.
- Apply Visual Management Techniques: Master the use of visual management tools to monitor, sustain, and improve Standard Work practices within the organization.
- Balance Workflow with Takt Time: Gain the ability to assess and adjust work sequences to balance workflow with takt time, improving efficiency and reducing bottlenecks.
Overview
Learning to See
How do you combine employee engagement, learning to see, elimination of waste, and creation of pull into your lean journey?
Go on a Snake Hunt! A snake will bite you if you see it, bite you if you hear it, and if you are around it long enough, it will bite you! Think of them as Safety Snakes, Quality Snakes, and 5S or something that might turn off the customer.
This Kaizen event will, without a doubt, become one of your winning best practices. One of the first steps towards educating associates in Lean is to help them see and identify waste. By seeing waste in a visual and competitive way, associates develop a much easier way to remember what they need to be looking for.
Benefits
- Enhanced Waste Identification: Employees develop the ability to quickly and accurately spot waste and inefficiencies in their work environment, leading to more effective operations.
- Proactive Problem Solving: By learning to see issues before they escalate, employees can take early action to prevent costly problems, improving overall operational efficiency.
- Increased Employee Engagement: The interactive and competitive nature of the Rattlesnake Hunt fosters team spirit and a stronger commitment to Lean practices.
- Improved Workplace Safety: Identifying and addressing safety hazards during the Rattlesnake Hunt helps create a safer work environment, reducing the risk of accidents.
- Sustained Continuous Improvement: The skills gained during the Rattlesnake Hunt can be applied continuously, driving long-term improvement and operational excellence across the organization.
Learning Objectives
- Identify and Visualize Waste: Develop the ability to recognize various forms of waste in the workplace, including safety hazards, maintenance issues, and inefficiencies, using visual management techniques.
- Enhance Observational Skills: Learn to see beyond daily routines to identify underlying problems that may not be immediately visible, improving the ability to detect issues before they escalate.
- Understand the Impact of Visual Excellence: Gain insight into how visual excellence can create the "WOW factor" in your operation, impressing both customers and employees.
- Manage by Exception: Learn to implement management by exception, where deviations from standards become immediately visible and prompt corrective actions.
- Foster Team Collaboration: Encourage team members to work together in identifying and addressing issues, promoting a culture of continuous improvement and shared responsibility.
- Apply Proactive Problem-Solving Techniques: Develop the skills to take proactive actions to eliminate issues before they create costs for the company, contributing to overall operational efficiency.
- Build Team Pride and Engagement: Understand how to create an environment where employees take pride in their work, leading to higher levels of engagement and commitment to excellence.
Overview
Continuous Flow and Pull Trigger / Kanban Workshop
The Continuous Flow and Pull Trigger / Kanban Workshop is designed to help organizations transition to a value-centric, pull-based system of planning and execution using Kanban. This workshop focuses on implementing the basics of Lean Kanban in various environments where work items are not known in advance. Participants will learn how to set up and manage a Kanban system, ensuring flexibility and efficiency in their planning and execution cycles.
Benefits
- Efficient Workflow Management: Learn how to split work into manageable pieces and define the stages of workflow.
- Visual Management: Display the status of all work items using Kanban boards, enhancing visibility and control.
- Improved Process Tracking: Determine and track the stages of work items, leading to better oversight and reporting.
- Enhanced Measurement: Gain the ability to measure and report on work progress effectively.
Learning Objectives
- Understand the basics of Lean Kanban.
- Learn how to shift to a value-centric pull-based system.
- Know when and how to use Kanban effectively.
- Master the essential elements of Kanban.
Overview
Value Stream Map Training
The Value Stream Map Training service offers a comprehensive, hands-on approach to mastering the creation and utilization of Value Stream Maps, essential for identifying inefficiencies and driving improvements in your processes. This workshop is structured in a "teach & do" format, guiding participants through the step-by-step process of gathering data, creating a Current State Value Stream Map, and developing a Future State Map using Lean tools like Standard Work, SMED, and Kanban. By participating, your team will gain the skills necessary to visualize the flow of materials and information, identify waste, and implement a strategic plan to achieve an optimized future state. This training not only equips your team with practical tools but also fosters a deeper understanding of how to continuously improve and sustain operational excellence.
Benefits
- Enhanced Process Visualization: Gain the ability to clearly visualize your current processes, making it easier to identify inefficiencies and areas for improvement.
- Improved Efficiency: Learn to identify and eliminate waste in your processes, leading to faster production times and reduced costs.
- Strategic Planning: Develop a clear roadmap for achieving future state goals with actionable steps and timelines.
- Cross-Functional Collaboration: Encourage teamwork by involving all relevant stakeholders in the mapping process, fostering a culture of continuous improvement.
- Informed Decision-Making: Use data-driven insights from the Value Stream Map to make informed decisions that align with your business objectives.
- Sustainable Improvements: Implement lasting changes that improve the overall flow of materials and information, leading to long-term operational excellence.
Deliverables
- Understand the Current State: Accurately assess and document the current state of your value stream, identifying key metrics and areas for improvement.
- Gemba Walk Execution: Learn to conduct effective Gemba walks to gather real-time data and insights from the actual work environment before creating the Future State map.
- Identify and Link Waste to Business Metrics: Recognize the 8 types of waste and link them to critical business metrics like Safety, Quality, Delivery, and Cost.
- Future State Mapping Techniques: Gain the skills to design a Future State Value Stream Map that reflects optimized processes and improved flow.
- Product and Information Flow Analysis: Develop an understanding of both product flow and information flow within your organization and how they interact.
- Conversion to Future State: Learn how to systematically convert the Current State map into a Future State map using Lean tools and methodologies.
- Change Management and Stakeholder Engagement: Learn how to circulate and communicate the Future State map effectively to gain input and drive change across the organization.
- Develop an Improvement Plan: Create a comprehensive improvement plan with clear steps, timelines, and responsibilities to achieve the desired Future State.
- Hands-on Practice: Apply the learned concepts by drawing both Current and Future State Value Stream Maps, reinforcing the training with practical exercises.
Overview
Quick Changeover Workshop
The Quick Changeover – SMED (Single-Minute Exchange of Dies) Training workshop introduces the essential steps for rapidly changing over equipment to provide a different product or service efficiently. This workshop combines lectures and hands-on training focused on decreasing changeover time in your current processes. The training applies to any industry that requires frequent changes in production or services, helping to reduce waste and improve efficiency.
Benefits
- Increased Efficiencies and Profitability: Learn how to significantly reduce changeover times using existing equipment, thereby increasing profitability without requiring additional capital investments.
- Reduced Inventory and Work In Process: Successful implementation leads to inventory reduction due to smaller lot sizes and less work in progress, improving overall efficiency.
- Improved Equipment Utilization Rates: Expect an improved equipment utilization rate, leading to quicker responses to customer orders and better operational flow.
Learning Objectives
- Understand and apply practical steps to reduce changeover time through hands-on applications on-site.
- Learn how to identify waste in the changeover process.
- Differentiate between internal and external time in changeover processes.
- Learn how to create a spaghetti diagram to visualize and optimize process flow.
- Develop techniques to shift internal time to external time and create standardized checklists to streamline operations.
Overview
Quality Stream Map Training
The Quality Stream Map Training workshop is designed to provide participants with hands-on experience in creating and analyzing a Quality Stream Map. This workshop focuses on identifying key quality metrics, understanding quality information flow, and developing a comprehensive plan to improve quality processes within an organization. Through the application of lean tools, participants will learn how to convert a Current State Quality Stream Map into a Future State Map, ensuring alignment with ISO standards and driving continuous improvement.
Benefits
- Visualize Quality-Related Issues: Gain a clear understanding of quality challenges and opportunities within the current processes.
- Identify Areas Needing Improvement: Learn to pinpoint critical areas that require immediate attention to enhance quality.
- Create a Future State Plan: Develop a structured plan for future improvements in quality processes, ensuring long-term success.
Learning Objectives
- Review and analyze the Current State Map of quality processes.
- Conduct a Gemba walk to understand quality checkpoints and identify improvement areas.
- Understand critical quality points that impact both suppliers and customers.
- Learn the flow of quality information, including non-conformance systems.
- Convert the Current State Quality Stream Map to a Future State Map.
- Draw and implement a comprehensive Future State Quality Stream Map.
- Integrate quality forms and coordinate with ISO systems.
- Develop an improvement plan that aligns with the Future State goals.
Overview
Total Productive Maintenance — TPM
Total Productive Maintenance (TPM) Training is designed to enhance the effectiveness and reliability of production machinery through a systematic approach that involves both maintenance personnel and production workers. The training focuses on transforming reactive maintenance into predictive maintenance, improving the overall maintenance process, and enhancing equipment management. The ultimate goal is to eliminate waste, reduce equipment failures, and ensure the smooth operation of machinery to maximize productivity and minimize downtime.
Benefits
- Enhanced Equipment Reliability: Transform reactive maintenance into predictive maintenance, leading to more reliable production machinery.
- Increased Productivity: Reduce breakdowns, defects, and minor stoppages, leading to improved machine speed and overall equipment effectiveness.
- Optimized Maintenance Processes: Implement systematic equipment improvement strategies, including early equipment management and autonomous maintenance, to ensure efficient and effective maintenance practices.
- Skill Development: Equip maintenance personnel with the skills needed to identify and eliminate waste, understand equipment failures, and build effective maintenance teams.
Learning Objectives
- Understand the causes and reasons behind equipment failures.
- Identify different types of equipment failures.
- Utilize root cause identification tools to diagnose issues.
- Measure equipment effectiveness and implement improvements.
- Build and manage an effective maintenance team.
- Use visual guides to enhance maintenance processes.
- Communicate TPM strategies effectively throughout the facility.
Overview
Visual Management
Visual Management is a critical component of any Lean Enterprise, driving long-term sustainability and continuous improvement. This service focuses on implementing Visual Management techniques to enhance daily operations, improve visibility of key metrics, and foster a culture of accountability. Through hands-on education and practical examples, participants will learn how to design and implement an effective Visual Management system that aligns with their organizational goals.
Benefits
- Enhanced Performance: Implement proven, sustainable visual processes that improve safety, quality, productivity, and delivery.
- Clear Communication: Facilitate smoother communication among team members and across departments.
- Employee Engagement: Increase employee involvement by providing visual cues that drive engagement.
- Improved Efficiency: Streamline processes and reduce lead times by making critical information visible and actionable.
- Value Stream Improvement: Support continuous improvement efforts and better management of value streams.
Learning Objectives
- Learn to design and implement your own Visual Management System.
- Gain visibility into waste and inefficiencies within processes.
- Understand how to create an Operational Excellence War Room.
- Develop skills in using visuals to see the big picture.
- Manage operations through Pipeline Visibility techniques.